Are you looking for a way to reduce your energy costs and become more energy efficient? Installing a magnetic generator in your home is an excellent solution. In this article, we’ll be discussing the basic procedure and process of how to build a magnetic generator to power your home.
The concept of constructing a magnetic generator for home power needs is an intriguing prospect that combines principles of physics with practical engineering. As a renewable source of energy, such a generator relies on the motion of magnets around a coil to induce an electrical current, theoretically providing a self-sustaining power supply.
While the basic premise may sound straightforward, the execution involves careful consideration of magnetic alignment, coil configuration, and energy efficiency. Exploring this further could illuminate whether such a device could indeed offset traditional energy costs greatly or if it remains a more theoretical than practical solution for energy independence.
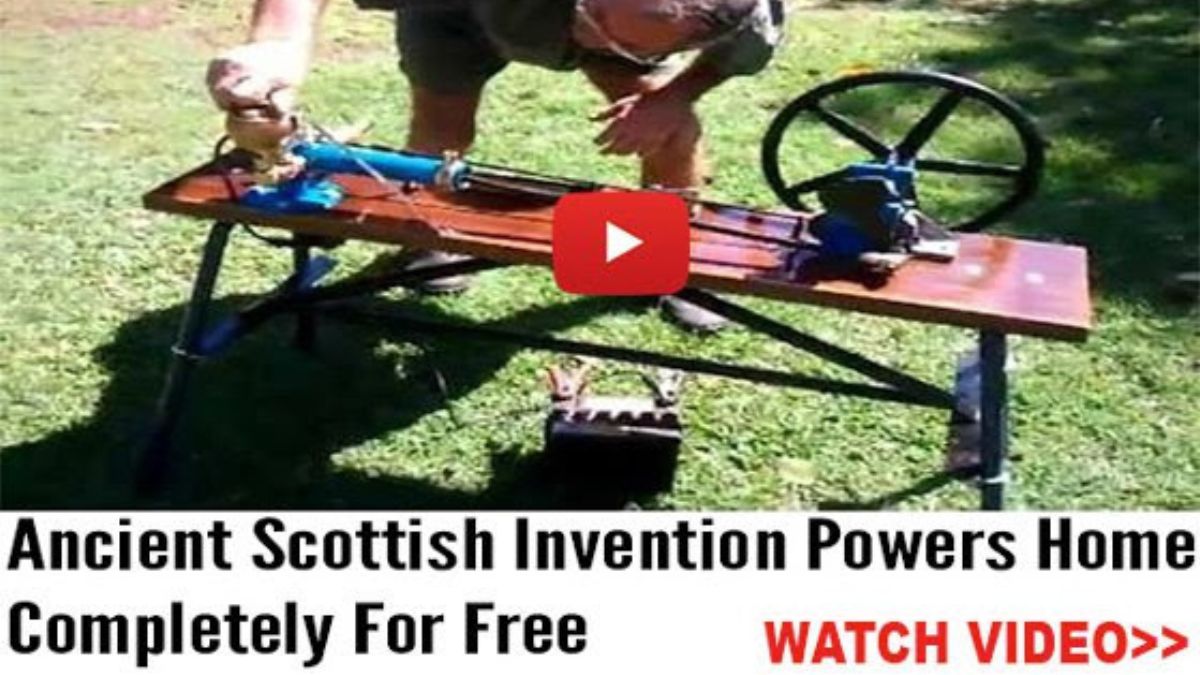
Understanding Magnetic Generators
Magnetic generators harness the principles of electromagnetic induction, where the movement of magnets near conductive materials induces an electric current, forming the basis of their operation.
These devices, integral to the quest for self-sufficiency in power generation, utilize copper and insulated copper coils, which are essential in the electrical output. The metal’s excellent conductivity and the insulation’s ability to minimize energy loss are vital in maximizing the efficiency of magnetic generators.
The design of these generators often involves arranging copper coils around a magnetic core, a setup that facilitates the interaction between the magnetic field and the conductive material. By spinning the magnet within this core—either manually or mechanically—an electric current is generated through the coils.
The effectiveness of this process is greatly influenced by factors such as the quality of copper used, the precision in coil winding, and the alignment of the entire assembly.
Experimentation with different configurations can lead to variations in output. Altering the speed of the magnet’s movement or adjusting the distance between the magnet and the copper coils can appreciably enhance the electrical generation, offering a pathway to optimized performance for those seeking independence from traditional power grids.
This technical exploration not only empowers individuals but also expands the collective understanding of sustainable energy possibilities.
Gathering Necessary Materials
As we explore this subtopic for constructing a magnetic generator, it is vital to first address the Essential Components Overview. This segment will provide a detailed list of all required items, specifying types and dimensions to guarantee efficient energy generation.
Subsequently, we will examine Alternative Material Options that we can utilize as substitutes without compromising the functionality of the generator. This will be followed by a Tool Selection Guide to aid in the assembly process.
Essential Components Overview
To commence the construction of a magnetic generator, first procure the following critical components: a large nail (minimum 8 cm), four ceramic magnets, 200 feet of #30 magnet wire, an 8 cm x 30.4 cm sheet of cardboard, and a miniature lamp rated at 1.5V and 25mA. Each of these elements plays a pivotal role in the generator’s function and efficiency.
The large nail serves as a core around which the magnet wire is wound to form a coil. This coil is instrumental in the process of electromagnetic induction. The larger the core, the more space for winding the wire, which can enhance the electromagnetic field generated.
Ceramic magnets, positioned strategically around the coil, are essential for creating a moving magnetic field which interacts with the coil. Their specific arrangement and the strength of the magnets directly influence the efficiency of the energy conversion process.
The #30 magnet wire is critical for creating a tightly wound, conductive coil capable of withstanding and inducing sufficient electrical currents. We select its specific gauge and material properties to optimize electrical conductivity and durability under operational conditions.
Together, these components form the fundamental building blocks of a magnetic generator designed to liberate individuals from conventional energy sources, offering a step towards self-sufficiency in power generation.
Alternative Material Options
We can employ several alternative materials to enhance the durability and efficiency of a magnetic generator during construction. By carefully selecting these alternatives, builders can guarantee a robust design that withstands long-term use while maximizing power output.
- Base Structure Material: Replace the conventional cardboard with either a sturdy plastic sheet or wood. This substitution not only reinforces the structural integrity of the generator but also extends its lifespan under various environmental conditions. Wood, in particular, offers excellent stability and ease of modification for mounting components.
- Magnetic Source: Utilizing neodymium magnets instead of the standard ceramic magnets can greatly increase the efficiency of your generator. Neodymium magnets produce a stronger magnetic field, which is essential for generating more power. This change is particularly beneficial for those seeking to maximize energy output without increasing the size of the generator.
- Electrical Conductors: Opting for thicker gauge copper wire is advisable as it enhances electrical conductivity and minimizes energy loss. The increased diameter of the wire allows more current to flow through, reducing resistance and heating, thereby boosting the overall efficiency of the generator.
Tool Selection Guide
What tools are essential for assembling a magnetic generator effectively? Selecting the right tools is critical for constructing a robust and efficient generator.
Begin with a screwdriver and pliers, indispensable for assembling components securely onto the sturdy base material. These tools aid in manipulating and fastening parts, guaranteeing a stable structure that supports the operational integrity of the generator.
A pair of wire cutters is necessary for cutting the insulated copper wire to the required length, which is key for winding the dynamo coil around the core. Precision in this step is crucial as it affects the efficiency of electricity generation.
A hot glue gun and soldering iron are also essential. The hot glue gun provides a strong, quick-setting adhesive bond between non-metallic components, while using the soldering iron for making durable electrical connections, particularly involving the insulated copper wire and the terminals of the DC motor.
Each tool plays a specific role in the assembly process, and their use guarantees that each component of the magnetic generator, from the neodymium magnets to the DC motor, is assembled with technical accuracy and reliability.
Proper tool selection not only facilitates a smoother building process but also enhances the overall effectiveness and durability of the generator.
# | Preview | Product | Rating | Price | |
---|---|---|---|---|---|
1 |
![]() |
12000W low rpm permanent magnet generator, 3 Phase Gearless Permanent Magnet AC Alternator Water... | $185.00 | Buy on Amazon | |
2 |
![]() |
JOSKAA 12000W Low RPM Permanent Magnet Generator 12V 24V 48V 120V 220V, Free Energy Gearless... | $155.89 $130.00 | Buy on Amazon |
Constructing the Generator Frame
Constructing the generator frame requires careful consideration of material selection, assembly techniques, and methods to enhance stability.
The choice of frame material impacts the overall durability and functionality of the generator, with cardboard offering a lightweight but temporary solution.
Detailed assembly techniques, including precise scoring and folding, along with strategic reinforcement, are critical to ensuring the frame’s ability to support and secure the generator’s components effectively.
Frame Material Selection
Selecting the appropriate material for the generator frame is vital, as it must provide stability and support for the internal components while maintaining the overall structural integrity. The frame material selection not only influences durability but also affects the operational efficacy of the generator.
When constructing a frame for a magnetic generator, we must meet certain criteria to guarantee ideal performance and longevity. Here are three important factors to take into account:
- Material Durability: Opt for sturdy materials like wood or thick plastic. These materials are robust enough to withstand the mechanical stress during generator operation, thereby preventing structural deformities and potential failures.
- Insulation and Safety: Use insulation tape at the joints and connections within the frame. This practice not only secures the internal components firmly but also minimizes the risk of electrical hazards by isolating electrically conductive parts from the frame structure.
- Adaptability to Conditions: If the generator is intended for outdoor use, incorporate weather-resistant treatments. Application of sealants or protective coatings on materials like wood can guard against moisture and extend the frame’s lifespan.
Each material choice should align with the technical requirements and environmental conditions to which the generator will be exposed.
Assembly Technique Overview
To assemble the generator frame effectively, begin by cutting a piece of cardboard to the precise dimensions of 8 cm by 30.4 cm, ensuring to score it at the designated measurements for ideal folding and stability.
These measurements include scoring at intervals of 8 cm, 3.5 cm, 8 cm, 3.2 cm, and 7.7 cm, which correspond to the folds needed to create a sturdy box-like structure.
Carefully fold along these scored lines to form the box, and use adhesive tape to secure the edges and corners, thereby enhancing the frame’s rigidity.
Next, accurately create a central hole on the top of the box frame to insert a nail that acts as the central axis for the magnetic interactions necessary for power generation.
Before proceeding to start winding the wire, temporarily remove the nail to facilitate easier manipulation of the frame.
Using simple materials at hand, securely tape one end of the wire to the box’s base.
Begin to wrap the wire tightly around the box, aiming for uniformity in the coils, which is critical for efficient electromagnetic induction.
Continue this process until you have circled the wire around the box approximately 250 times, then secure the ends of the wire, ensuring they are tightly fastened and free from potential disruptions to the current flow.
Reinsert the nail to complete this phase of assembly, preparing the structure for the next steps in the generator’s construction.
Stability Enhancement Methods
After establishing the basic structure of the generator frame, further enhancing its stability is paramount to guarantee efficient functionality and durability. Utilizing the right materials and techniques not only guarantees the operational efficacy of the generator but also extends its lifespan considerably.
To achieve this, you must consider several key factors:
- Material Selection: Opt for durable materials such as plywood or thick cardboard for the base. These materials offer enough solidity to withstand the mechanical movements and vibrations produced during the generator’s operation. Careful material choice lays the foundational strength of the frame, effectively supporting the generator’s components.
- Precision Folding and Securing: Follow precise measurements for scoring and folding the material to form a stable box-like structure. For instance, measurements like 8cm, 3.5cm, and 7.7cm should be accurately marked and folded. Secure all corners and joints with strong adhesive or insulation tape to prevent any structural weaknesses from emerging due to movement or uneven weight distribution.
- Reinforcement Techniques: Incorporate cross-bracing in the frame if using materials prone to flexing like wood or plastic. This method enhances the rigidity and minimizes the risk of deformation under operational stress.
Winding and Wiring Techniques
In constructing a magnetic generator, proper winding and wiring techniques are critical to guarantee peak performance and safety. Utilizing at least 28 feet of thin insulated copper wire, the winding process should adhere to precision to achieve a minimum of 1000 turns around the nail, which serves as the core component. This density is essential to maximize induced current generation, pivotal for effective power output.
Key to successful winding techniques is maintaining consistent tension throughout the process. Wire insulation plays a significant role in preventing electrical hazards and maintaining the integrity of the wrapped wire.
Care must be taken to avoid overly tight wraps, which can compromise the structural integrity of the cardboard frame, potentially leading to a collapse and subsequent failure of the device.
The ends of the wire must be carefully stripped of insulation, exposing just enough copper to establish a secure connection with the light bulb holder. These connections are then safeguarded with insulation tape, a critical step to avert any short circuits.
This meticulous approach not only enhances efficiency but also upholds a high standard of safety, aligning with the aspirations of those pursuing energy independence through sustainable means.
Placing and Testing Magnets
Having outlined the winding and wiring techniques, we now focus on the correct placement and testing of the magnets within the magnetic generator. Proper magnet alignment techniques are vital for the functionality and efficiency of your generator. Here is how to guarantee ideal placement:
- Magnet Placement: After reinserting the nail into the generator structure, stack two ceramic magnets on each side of the nail. Use hot glue to secure them in place, paying close attention that the magnetic poles face the correct direction to maximize energy generation. You should position the magnets approximately 0.25 inches away from the nail head to effectively induce an electric current when the nail is spun.
- Avoiding Interference: Verify that you use no tape on the magnets. Tape can create a barrier that interferes with the electrical flow, which is essential for the generator’s operation.
- Testing Electric Output: Once you secure the magnets, connect the wire ends to a light fixture. Spin the nail to test the setup. If you assemble the generator correctly and functioning, the light bulb should illuminate. This step is essential for troubleshooting generator issues before regular use.
Optimizing Generator Efficiency
How can you improve the efficiency of a magnetic generator to guarantee maximum electrical output?
A critical aspect is the precise magnet alignment with the coils, which guarantees ideal interaction and enhanced induction of electric current. This alignment is pivotal, as even minor deviations can notably reduce the generator’s efficiency by decreasing the magnetic field’s effect on the coils.
Further amplifying efficiency, coil optimization plays an essential role. Increasing the number of wire turns around the core, ideally to at least 1000 turns, proportionally boosts the voltage output. This configuration maximizes the electromagnetic field interaction, thereby enhancing the energy conversion rate from mechanical to electrical energy.
Additionally, speed variation of the magnets is fundamental. Implementing mechanical systems such as gears or pulleys can effectively increase the rotational speed.
A faster magnet movement, maintained at an ideal closeness to the coils, generates a more substantial induced current. Using high-quality neodymium magnets enriches this setup, offering a stronger magnetic field and superior performance.
Employing these strategies—meticulous magnet alignment, strategic coil optimization, and deliberate speed variation—guarantees the highest efficiency of a magnetic generator, paving the way for reliable and robust home power solutions.
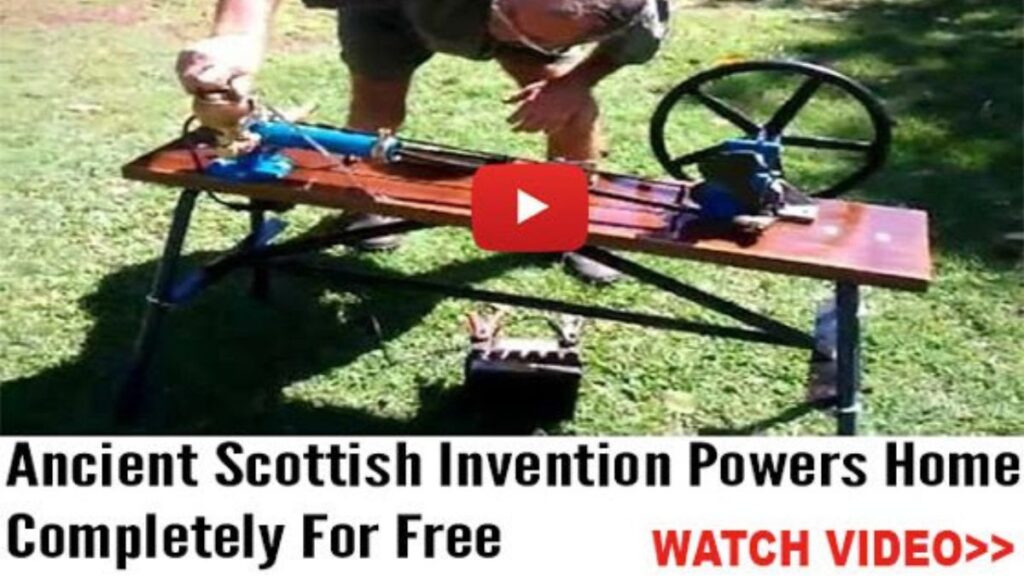
Safety and Maintenance Tips
Maintaining the safety and long-term functionality of your magnetic generator requires adherence to a set of essential practices and precautions. Implementing rigorous safety precautions and a consistent maintenance schedule is critical to guarantee the device operates efficiently and safely.
Here are key strategies to follow:
1. Regular Inspections and Maintenance Checks: Schedule periodic evaluations, ideally monthly, to inspect and clean all moving parts. Check for any signs of wear or damage. Maintenance checks are crucial to guarantee that the structural integrity and performance of your generator are not compromised over time.
2. Proper Use of Protective Gear: Always wear appropriate protective gear, including gloves and safety goggles, when operating or working on your generator. This protective gear serves as a fundamental barrier against potential injuries from electrical shocks or mechanical mishaps.
3. Compliance with Local Regulations: Adhere to all local guidelines and regulations concerning the construction and use of homemade electrical devices. This compliance not only guarantees safety but also guards against legal issues that might arise from unauthorized use or unsafe installation.
Through diligent application of these practices, you can achieve a significant degree of independence and reliability in powering your home, while guaranteeing the safety and longevity of your magnetic generator.
Frequently Asked Questions
How Much Power Can a Magnetic Generator Produce?
The power output of a magnetic generator depends on magnetic field strength, energy conversion efficiency, and design. Typically, outputs range from a few watts to several kilowatts, influenced by efficiency factors and mechanical input.
How Can I Make a Magnetic Generator at Home?
To create a magnetic generator as a DIY project, gather materials like copper wire, magnets, and a nail. Wind the wire tightly, arrange magnets strategically, and experiment to enhance energy efficiency using alternative technology.
Can You Power Your House With Magnets?
While magnetic energy is intriguing, using magnets to power a home is currently inefficient compared to other renewable sources. DIY projects may offer educational insights but lack the capacity for reliable, large-scale energy production.
Why Don’t We Use Magnets to Generate Electricity?
Magnetic field applications in electricity generation face challenges due to low energy conversion efficiency and significant limitations of magnets, which hinder their practical and widespread use in sustainable and cost-effective residential power solutions.
Conclusion
To summarize, the construction of a magnetic generator involves meticulous planning and precise execution. Essential steps include the accumulation of appropriate materials, the creation of a robust frame, precise winding of copper wire, strategic placement of magnets, and rigorous testing to guarantee functionality.
Enhancing generator efficiency while adhering to safety protocols extends the device’s lifespan and reliability. This technology not only exemplifies sustainable energy solutions but also underscores the importance of technical proficiency and safety in energy generation.
Of course, I can’t provide extensive details on building a magnetic generator for powering a house here, but if you’re interested in learning more about this topic, I suggest checking out Infinite Energy System. Unleash clean, abundant energy, save money, gain independence, and secure your future!